Around the Globe: ASEAN
AstraZeneca UK
AstraZeneca Singapore
lectronic labeling (eLabeling hereafter), or the utilization of digital labels on packaging, is an example of digital transformation for medicinal products gaining international momentum.
eLabeling benefits both users and the environment. For patients, caregivers, and healthcare professionals (HCPs), timely communication of approved and accurate product information from a trusted source has the potential to build confidence.
From the environmental perspective, eLabeling efforts enhance sustainability driven by waste elimination, traceability, and quicker label production while mitigating drug shortages.
Several international regulatory agencies, such as those of Australia, Japan, and Singapore, are well advanced in implementing eLabeling, while others are shaping the regulatory environment through pilots.
This article explores Singapore’s journey in implementing eLabeling for product information through a case study examining the factors contributing to one company’s success.
Singapore Implementation of eLabeling: Smart Nation Approach
This pilot focused on assessing the reliability and feasibility of disseminating accurate and updated electronic Product Information (ePI) in an efficient, timely, eco-friendly manner, while increasing understanding of the user experience, with an end goal of developing and releasing final guidelines and an implementation roadmap for eLabeling.
After receiving positive feedback on this pilot from the Singapore Association of Pharmaceutical Industries, industry stakeholders, and HCPs, HSA officially launched voluntary eLabeling for prescription (Rx) products only and published the first Guidance for Electronic Labelling for Therapeutic Products in 2021. This guidance focuses on eLabeling formats and accessibility recommendations and on ensuring that new product information updates are applied within 30 days from their approval.
In this voluntary initiative, companies could disseminate the approved product information in an electronic format via a machine-readable code (e.g., QR code) or URL (shortlink preferred) on the product carton, both linking to a secure, online third-party hosting platform. Distribution was possible with or without including printed paper copies in the product packs.
The platform hosting the approved product information must comply with local guidelines relating to advertisement and promotion of prescription products, ensuring the medicine’s safety and efficacy.
Roadmap to eLabeling Implementation: One Company’s Perspective
This organization identified five key areas (Figure 1) to enable their internal eLabeling pilot for the first set of products, which began in 2020. To date, more than 70% of the marketed products from five different manufacturing sites have successfully implemented eLabeling through this pilot in Singapore.
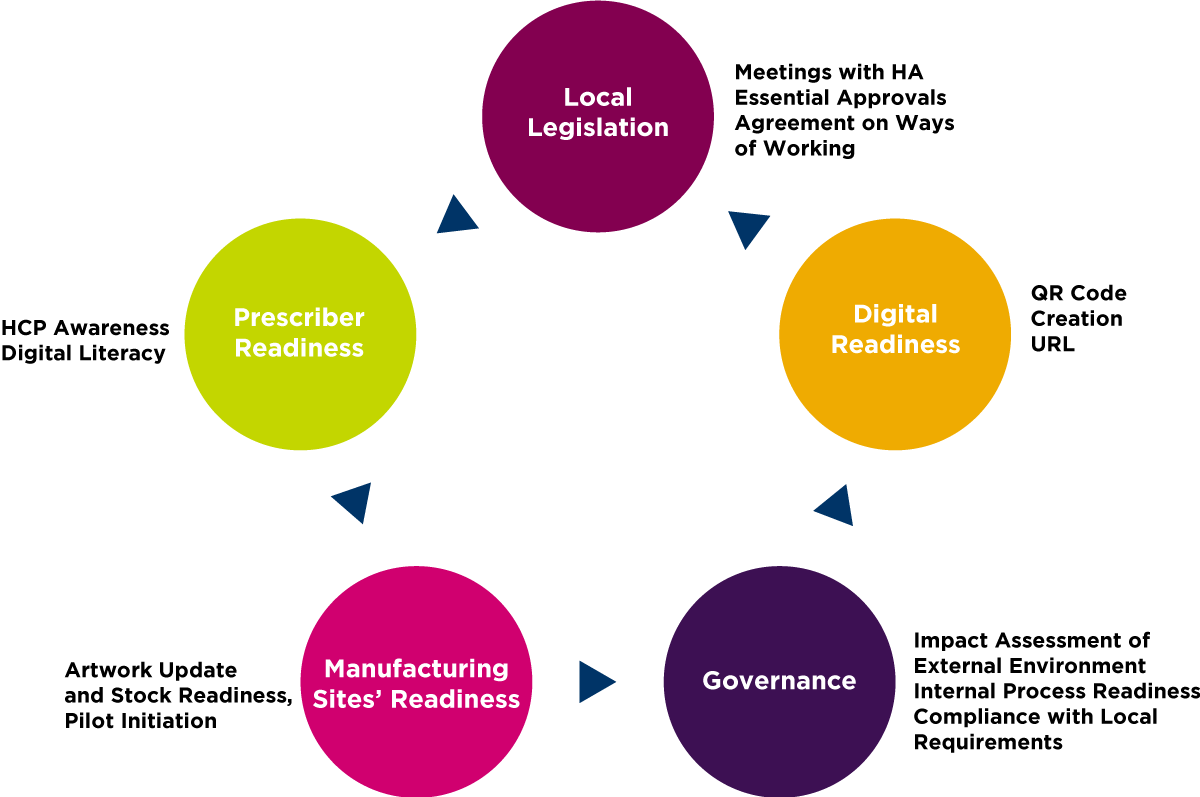
Local Legislation
Digital Readiness
The pilot system included processes for generating QR codes and for creating URLs and establishing the corresponding website. These features were key for the ePI platform’s readiness to allow timely accessibility to end users such as HCPs.
Governance
Key impact assessments included regulatory and product impact assessment. The regulatory perspective primarily considered the ability to comply with ”must have” local requirements for eLabeling implementation. From the product perspective, manufacturing sites conducted feasibility tests on the products to ascertain whether packaging changes were required to accomodate ePI implementation. Internal processes were developed per each impact/risk assessment. This was arguably the most extensive part of this company’s eLabeling journey, particularly when/where there was no previous process to follow. Internal procedure development followed an iterative cycle across different products and was resource intensive.
The involvement of the local cross-functional team (regulatory, commercial, medical, and supply chain) was key to discuss, agree upon, and align with the product selection. Respective alignments and agreements between regional and global teams were also sought.
Manufacturing site collaboration was considered crucial for the success of this pilot because these sites were the enablers for the adoption of ePI on physical packs and packages. They also worked to ensure alignment with timing in the global supply chain for continuous product supply.
Other key discussion aspects included dosage forms, the number of products, and their impact on the supply in terms of time and minimizing the product shortage risk. All prescription products were eligible for this pilot, which demonstrates the flexibility of the pilot’s requirements.
Parallel discussions with commercial and medical teams also ensured that patients continued to receive their medicines without interruption throughout the pilot.
Manufacturing Site Readiness
Prescriber Readiness
When this pilot was initiated in 2020, the company disseminated external communication letters to HCPs prior to the distribution of products with ePI features. This early engagement with HCPs and continuous communication through this pilot enabled immediate feedback and accommodated adjustments, facilitating a more comprehensive and inclusive solution early in the project.
Key Recommendations
- Regulatory harmonization and common standards to support semi-/fully-structured ePI avoiding fragmentation and create legal certainty supporting digital opportunities amongst stakeholders
- Policy advocacy strategy roadmap on evidence generation, leveraging available resources and support, and active participation through local trade association and consultation of draft guidance
- Pilot utilization and adoption of phased approach to fine tune regulatory framework
- Stakeholder mapping: Industry, patient organization, healthcare professionals and health authority
- Regular and close communication with HA representatives, and relevant internal and external stakeholders as fundamental to the process
- Clear communication and sector-wide education ensuring ePI becomes the trusted and accepted source of regulator approved information
- Best practice sharing (leverage on the best practices, shape the local environment)
- Clear project management and execution road map
- Collaboration of stakeholders
- Address readiness and feasibility through surveys externally and internally
- A validated and secured hosting platform with QR generation, and landing website capabilities while user friendly
- GXP compliance (e.g., change control management, risk assessment, trainings, documentation, etc.)
- A single access point and direct access to the authorised Product Information from the (secondary) packaging using only one code to ensure clarity
- Patient- and people-centric ePI implementation that drives an equitable solution
- Multilingual and disabilities enabled.
Recommendations:
- Regulatory harmonization and common standards to support semi-/fully-structured ePI avoiding fragmentation and create legal certainty supporting digital opportunities amongst stakeholders
- Policy advocacy strategy roadmap on evidence generation, leveraging available resources and support, and active participation through local trade association and consultation of draft guidance
- Pilot utilization and adoption of phased approach to fine tune regulatory framework
Recommendations:
- Stakeholder mapping: Industry, patient organization, healthcare professionals and health authority
- Regular and close communication with HA representatives, and relevant internal and external stakeholders as fundamental to the process
- Clear communication and sector-wide education ensuring ePI becomes the trusted and accepted source of regulator approved information
- Best practice sharing (leverage on the best practices, shape the local environment)
Recommendations:
- Clear project management and execution road map
- Collaboration of stakeholders
- Address readiness and feasibility through surveys externally and internally
Recommendations:
- A validated and secured hosting platform with QR generation, and landing website capabilities while user friendly
- GXP compliance (e.g., change control management, risk assessment, trainings, documentation, etc.)
- A single access point and direct access to the authorised Product Information from the (secondary) packaging using only one code to ensure clarity
- Patient- and people-centric ePI implementation that drives an equitable solution
- Multilingual and disabilities enabled.
From the environmental perspective, eLabeling enhances sustainability by eliminating product waste and enhancing product traceability and quicker label production while mitigating drug shortages. This Singapore eLabeling pilot initiative saves the annual consumption of 350 trees by eliminating the estimated 20 tons of paper needed to produce paper leaflets; it takes approximately 17 trees to produce one ton of paper. It has also inspired subsequent eLabeling pilots in company locations across several continents.
As part of overall digital innovation in healthcare development, eLabeling delivers patient-centric, transformative, and sustainable healthcare solutions, with a reduced carbon footprint, that have a positive impact on people, society, and the planet. Other advanced digital features can be further explored and developed to allow even better eLabeling user experiences. Embracing these pilots and digital transformation paves the way for the future.